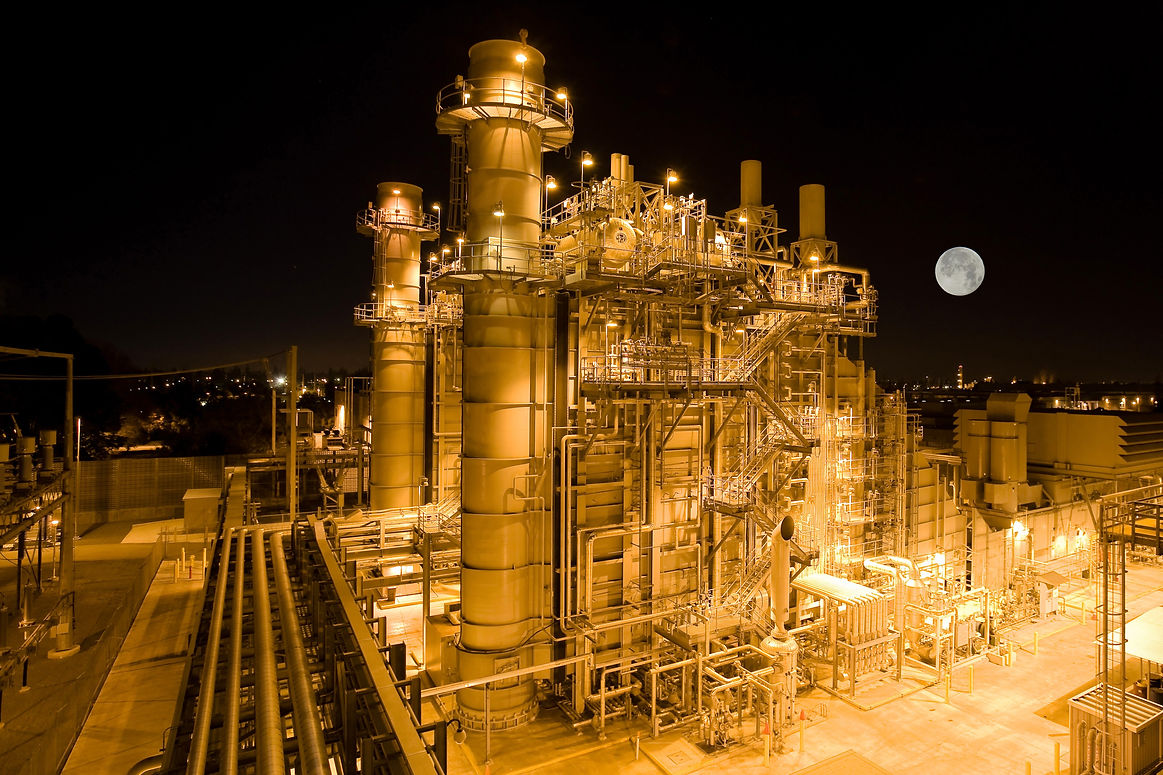
Air Leak Management
Compressed air leak inspection involves a comprehensive assessment of a system that utilizes compressed air, with the aim of identifying and addressing any leaks within the system. This study typically includes the following steps:
1. Inspection: Our engineers inspect the entire compressed air system, including pipes, fittings, valves, and other components, to locate potential leaks.
2. Measurement: Specialized equipment is used to measure air pressure, flow rates, and other relevant parameters to pinpoint the locations and severity of leaks.
3. Detection: Various methods, such as ultrasonic leak detection or thermal imaging, may be employed to identify leaks that might not be visible to the naked eye.
4. Analysis: The data collected during the study is analyzed to determine the impact of the leaks on energy consumption, system efficiency, and overall operational costs.
5. Reporting: A detailed report is generated, highlighting the locations of leaks, their sizes, potential energy savings, and recommended actions for repair.
6. Repair Recommendations: Based on the findings, the study provides recommendations for addressing the identified leaks, which could include repairing or replacing faulty components.
7. Cost Savings: The study often calculates the potential cost savings that can be achieved by fixing the leaks, which can be a compelling incentive for taking action. A compressed air leak study aims to improve the efficiency and sustainability of a system by reducing energy waste caused by leaks. It can lead to significant financial savings and a more environmentally friendly operation.
Comprehensive Compressed Air Leak Inspections
Uninterrupted Evaluations for Optimal Efficiency
We extend our services to encompass compressed air leak inspections during weekends, holidays, and third shifts. Certain clients opt for these inspections during periods when the compressed air system remains charged, and plant operations are temporarily halted